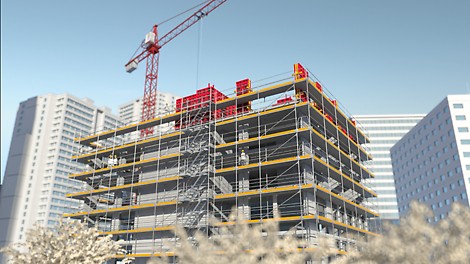
All Products
Use the filter function below to find the product you're looking for and its application.
Interested in learning more about our products?
Contact us – we will be happy to help you.
Use the filter function below to find the product you're looking for and its application.
Contact us – we will be happy to help you.